Fraunhofer CCPE at the IFAT 2024
Chemical recycling: technology transparency and investment security required
The VDMA and the Fraunhofer Cluster of Excellence Circular Plastics Economy CCPE are presenting the Chemical Recycling Spotlight Area at IFAT. Technologies for the recycling of plastics that can complement established mechanical processes will be presented, including solvent-based processes, solvolysis, pyrolysis and gasification.
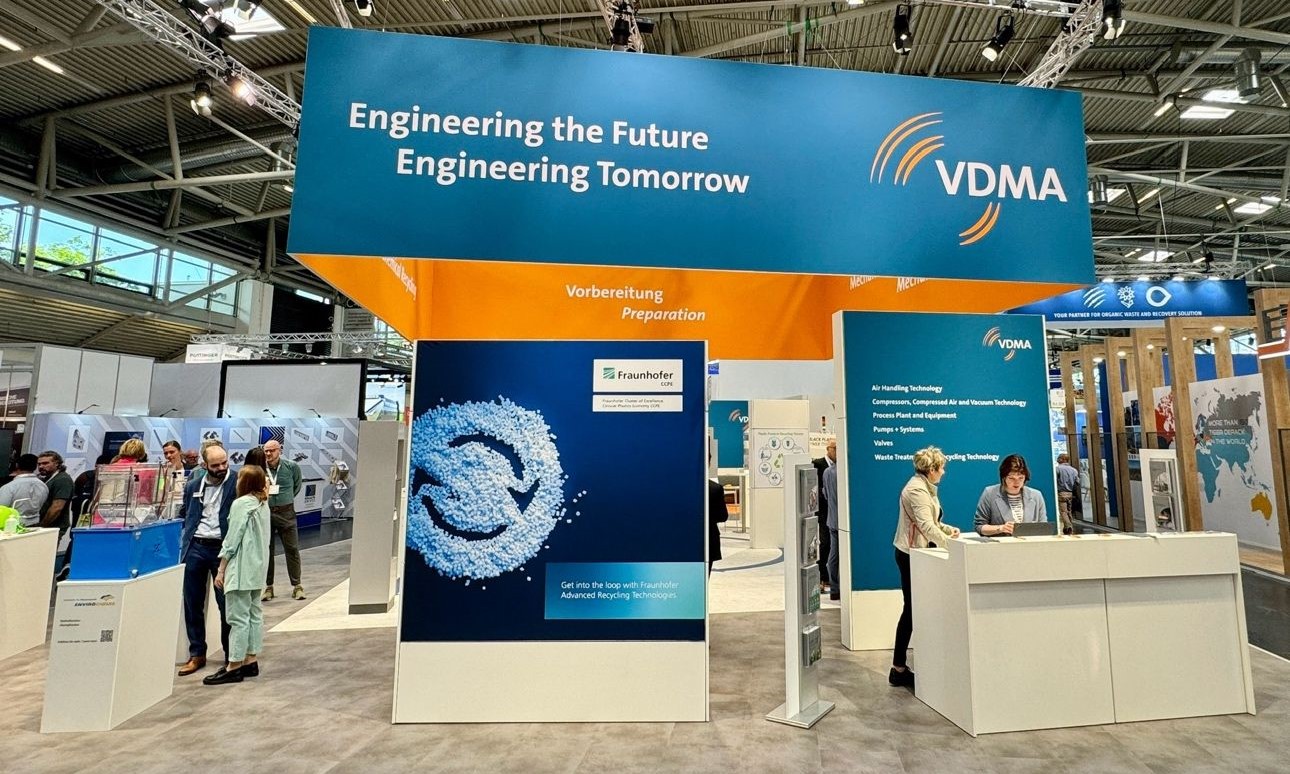
According to the EU targets, 60 per cent of everyday waste collected and treated by local authorities must be reused or recycled by 2030. In addition, stricter rules for the shipment of waste to third countries were adopted in February 2024: the export of plastic waste to non-OECD countries will be prohibited and stricter conditions for exports to OECD countries are expected. In order to fulfil these requirements, recycling capacities in Europe must be expanded, especially for waste streams that currently end up in incineration.
‘The circular economy must be considered holistically. Starting with the collection, sorting and treatment of waste through to processing. This is not possible without mechanical engineering and its solutions. Whether shredders, reactors or extruders - process engineering provides the technology for chemical recycling. We are in favour of an open-technology approach,’ says Richard Clemens, Managing Director of the VDMA Process Plant and Equipment.
The Fraunhofer Cluster of Excellence Circular Plastics Economy CCPE combines the expertise of six institutes of the Fraunhofer-Gesellschaft and cooperates closely with partners from industry. Together, systemic, technical and social innovations are developed that focus on the life cycle of plastic products from design to end-of-life.
Prof. Dr.-Ing. Manfred Renner, head of the cluster, says: ‘For a circular plastics economy, we need a substantial transformation of the entire value chain. This starts with product design, keyword eco-design, and extends to business models, materials, manufacturing processes and the utilisation of the product through to the question of what happens at the end of the life cycle. When other R-strategies, such as remanufacturing, repair or refurbishment, etc. no longer work, recycling comes into play. The special thing about chemical recycling is that it allows plastics that can no longer be mechanically processed to be returned to the cycle. The value chain from plastic waste to recycled virgin material is closed. If this requirement, i.e. virgin material quality, can be met via mechanical recycling, this should be done - if not, we should continue to develop and utilise the technologies that make this possible.’
Several technologies that are being developed and refined at the Fraunhofer CCPE institutes are now on the threshold of market maturity, e.g. solvent-based processes or thermochemical approaches such as pyrolysis. Market observers assume that the number of new plants will rise sharply over the next five years; in Europe alone, more than 40 plant projects are currently being planned in 13 countries.
Prof. Dr.-Ing. Matthias Franke, Head of the Sulzbach-Rosenberg branch of Fraunhofer UMSICHT, where the focus is on developing thermochemical recycling methods and downstream processes, focuses on the product quality of recycled plastics: ‘Even today, the demand for high-quality recycled plastics cannot be met. That's why we need new, innovative recycling processes in addition to the tried-and-tested mechanical methods. This will enable us to utilise plastic waste that has previously only been used for energy recovery, for example composite materials, shredder residues or heavily contaminated, additive-laden waste. At the same time, a recyclate quality can be achieved that is virtually equivalent to that of virgin material. Chemical recycling technologies in combination with suitable pre- and post-treatment steps offer enormous potential here - especially if it is possible to find the most effective process or the best combination for the different input streams. This is technically feasible. The task now is to create the framework conditions for investment and to start practical implementation. Applied research, the industry, in particular the mechanical and plant engineering sector, and politics are equally in demand here.’
This view is also shared by the VDMA: in the coming years, an investment-friendly environment is needed, secured by sensible political framework conditions.
As far as the choice of processing technology is concerned, technology providers, machine and plant manufacturers and the future operators of recycling plants are currently looking for the sweet spot between the available input stream, recycling processes including pre- and post-treatment, the desired recyclate quality, cost-effectiveness and sustainability. There will be no one-size-fits-all solution for the different waste streams. Fraunhofer CCPE assumes that smart process combinations or process cascades consisting of two or more processes will prevail. This would allow even complex waste mixtures to be treated almost completely, while at the same time achieving an optimised yield and quality of recyclates.
Last modified: